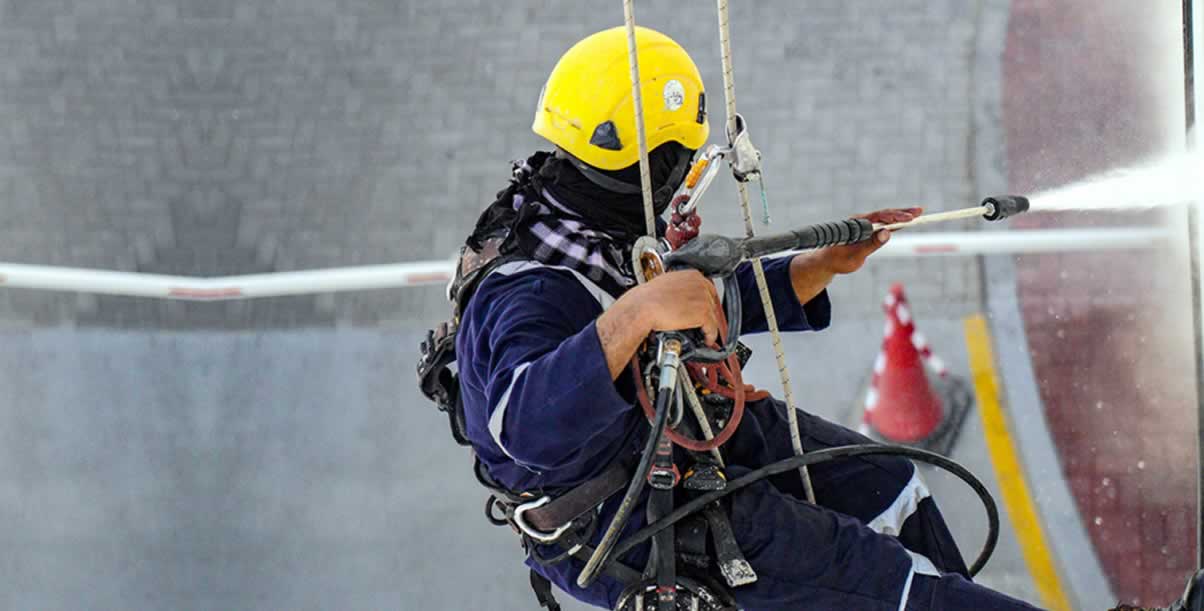
Introduction
In the world of industrial applications, water jetting and water blast processes have emerged as powerful tools, utilizing the force of water to perform a diverse range of tasks, from cleaning and surface preparation to cutting through the toughest materials. This blog explores the principles, methods, and applications of water jetting and water blast, highlighting their advantages and environmental benefits. Additionally, we’ll discuss the crucial role of Parker Polyflex Certified Assembler and the benefits it brings to these applications.
I. The Science Behind Water Jetting and Water Blast
Water Jetting Principles
Water jetting involves using a high-pressure water stream to clean surfaces and remove unwanted materials. Fluid dynamics play a significant role, where water is pressurized and expelled through a small nozzle at extremely high velocities. This creates a focused stream of water that exerts tremendous force on the target surface, effectively removing contaminants, coatings, and debris. High-pressure water acts as a powerful cutting agent, enabling precision cleaning and surface preparation.
The water pressure used in water jetting can vary depending on the application. Low-pressure water jetting is used for cleaning delicate surfaces or removing light coatings, while high-pressure water jetting is employed for more demanding tasks, such as removing heavy corrosion, paint, or tough industrial residues.
Water Blast Techniques
Water blasting, also known as hydro blasting or water cutting, takes water jetting to another level by utilizing significantly higher water pressures. In water blast applications, water pressures can exceed 40,000 psi (pounds per square inch), making it possible to cut through various materials, including thick metals, concrete, and stone.
Water blasting focuses a highly pressurized water stream through a jewel orifice, creating an intense cutting force that allows for precise and intricate cutting. Unlike traditional cutting methods generating heat and causing heat-affected zones in the material, water blasting produces minimal heat, making it ideal for materials sensitive to temperature changes.
II. Applications of Water Jetting and Water Blast
Industrial Cleaning and Surface Preparation
Water jetting is widely used for industrial cleaning and surface preparation across various industries. Providing an eco-friendly alternative to chemical cleaning methods, water jetting reduces environmental impact and improves worker safety. It effectively removes rust, paint, and graffiti from buildings, bridges, and structures. Additionally, it cleans industrial equipment and machinery, enhancing performance and extending lifespan.
Water jetting is essential for achieving proper adhesion of coatings and repairs in surface preparation applications. It removes contaminants, loose material, and surface imperfections, creating a clean and profiled surface that enhances the bonding strength of subsequent coatings and repairs.
Cleaning and Maintaining Pipelines
Water jetting plays a critical role in cleaning and maintaining pipelines, including oil and gas, water utilities, and petrochemical plants. Over time, pipelines accumulate deposits, sediments, and debris, leading to reduced flow capacity and operational inefficiencies.
High-pressure water jetting clears blockages, removes scale, and cleans interior pipeline surfaces. It ensures the smooth flow of fluids, reduces the risk of pipeline failures, and prolongs infrastructure life.
Ship Hull Cleaning
Water jetting is extensively employed in the maritime sector for ship hull cleaning and maintenance. Over time, marine organisms like barnacles, algae, and mollusks adhere to hull surfaces, causing drag and reducing fuel efficiency.
With higher pressures, water jetting effectively removes marine fouling, ensuring smooth sailing and improved fuel economy. Regular hull cleaning with water jetting prevents the spread of invasive species between water bodies, contributing to marine ecosystem conservation.
Concrete Surface Preparation
Water jetting is invaluable for preparing concrete surfaces before repairs or coatings. In concrete surface preparation, it removes deteriorated concrete, loose particles, and contaminants. This process is crucial for successful and long-lasting repairs.
The absence of heat generation during water jetting ensures surrounding concrete remains intact and free from damage, minimizing the risk of additional repairs. Additionally, it eliminates the need for abrasive methods, which can cause surface roughness and improper coating adhesion.
Industrial Cutting
Water blast applications offer precise cutting capabilities with minimal heat-affected zones. The versatility of water blasting makes it ideal for aerospace, automotive, and construction industries, where precision cutting is essential for complex components and structures.
Water blasting effectively cuts intricate shapes and patterns, suitable for materials sensitive to temperature changes, ensuring minimal distortion and accurate cutting results.
Demolition and Concrete Removal
Water blasting offers a safer and more precise alternative to traditional methods for controlled demolition and concrete removal. Hydrodemolition, a specialized technique, removes concrete from structures without damaging reinforcing steel.
Hydrodemolition targets concrete removal, making it ideal for bridge deck rehabilitation, concrete repair, and renovation projects.
Mining and Excavation
In the mining and excavation sectors, water jetting removes overburden, loosens ore, and breaks rocks. High-pressure water jets cut or break rocks, allowing easier excavation and ore extraction. Reducing the need for explosives minimizes environmental impact, vibration, and safety hazards.
Water jetting cleans tunnels, removes debris, and enhances excavation surface stability.
III. Advantages of Water Jetting and Water Blast Applications
Precision and Versatility
Water jetting and water blast technologies offer unparalleled precision, ideal for intricate cutting and surface preparation tasks. These systems are customizable for various materials and applications, enhancing industrial process versatility.
Water blasting produces clean and precise edges, minimizing the need for secondary finishing processes. Its ability to cut intricate shapes and patterns suits industries requiring complex component fabrication.
Environmental Friendliness
Using water as the primary force in water jetting and water blast applications makes them environmentally friendly. Unlike traditional methods with chemicals or abrasive materials, they generate no harmful by-products or emissions, reducing environmental impact.
Water jetting and water blast applications significantly reduce hazardous waste production, as they rely on water and sometimes abrasives with no harmful residues requiring special disposal. Lower waste management costs align with environmental regulations and waste reduction goals.
Operator Safety
Water jetting and water blast applications prioritize operator safety with reduced exposure to hazardous chemicals and elimination of heat-intensive processes. High-pressure water minimizes the risk of chemical exposure and related health hazards, ensuring a safer work environment.
Water jetting and water blast techniques are free from risks like noxious fumes, fire, or explosions, suitable for confined spaces or hazardous work areas.
Cost-Effectiveness
Water jetting and water blast applications lead to long-term cost savings for industries. Precision cutting and reduced material wastage result in improved material utilization, lowering production costs.
Heat-affected zones absence extends cutting tool life, reducing frequent replacements and maintenance. Water jetting performs multiple tasks with a single setup, minimizing downtime and labor costs, optimizing operational efficiency.
IV. The Importance of Parker Polyflex Certified Assembler
As water jetting and water blast applications become more prevalent in various industries, ensuring proper maintenance and service of equipment is crucial for optimal performance and safety. This is where the role of a Parker Polyflex Certified Assembler becomes invaluable.
A Parker Polyflex Certified Assembler undergoes specialized training and certification provided by Parker Hannifin, a leading manufacturer of high-pressure hoses and related products. These assemblers possess in-depth knowledge of Parker’s products, best practices, and safety standards, making them experts in servicing and assembling water jetting and water blast equipment.
Benefits of Working with Parker Polyflex Certified Assembler:
Expertise: Certified assemblers have a comprehensive understanding of Parker’s high-pressure products and technologies. Their expertise ensures equipment assembly, maintenance, and optimal performance.
Safety: Safety is a top priority for Parker Polyflex Certified Assemblers. They adhere to strict safety guidelines, reducing accidents and injuries during equipment operation.
Reliability: Certified assemblers ensure equipment is serviced with precision and quality, providing consistent and reliable performance, minimizing downtime and maximizing productivity.
Compliance: Working with a certified assembler ensures equipment meets industry standards and regulations. Compliance is essential for a safe and legal operation.
Product Warranty: Using a Parker Polyflex Certified Assembler may be necessary to maintain the manufacturer’s product warranty. This protects the investment and provides peace of mind.
Custom Solutions: Certified assemblers offer custom solutions tailored to specific applications, recommending suitable high-pressure hoses, fittings, and accessories for water jetting and water blast equipment.
Timely Service: Certified assemblers provide efficient and timely service, reducing equipment downtime and maintaining smooth operations.
Conclusion
Water jetting and water blast applications have revolutionized industrial cleaning, surface preparation, and cutting processes. The power of water, harnessed through advanced technologies, offers precision, safety, and environmental benefits that traditional methods cannot match. The significance of water jetting and water blast applications, along with the expertise of Parker Polyflex Certified Assemblers, will only grow as industries prioritize sustainability and efficiency, providing a cleaner and safer future for industrial processes worldwide.
By working with a Parker Polyflex Certified Assembler, industries ensure optimal performance, reliability, and safety of their water jetting and water blast equipment, further enhancing the efficiency and effectiveness of these powerful liquid force applications. The expertise of certified assemblers ensures high-pressure hoses and fittings meet quality standards, providing custom solutions and timely service to maximize productivity and cost-effectiveness. Embracing the power of water jetting and water blast applications, in tandem with the expertise of certified assemblers, paves the way for a more sustainable and advanced industrial landscape.